Vše o sváření a svařování
Svařování nebo sváření je proces, který slouží k vytvoření trvalého, nerozebíratelného spoje dvou a více součástí. Obecným požadavkem na proces svařování je vytvoření takových termodynamických podmínek, při kterých je umožněn vznik nových meziatomárních vazeb. Prakticky je velmi obtížné dosáhnout spojení na úrovni meziatomových vazeb za okolních podmínek - běžná teplota a tlak, kdy je termodynamický stav materiálů stabilní respektive metastabilní.
Je nutné tento termodynamický stav změnit. Proto je při svařování nutné působit buď tlakem, teplem nebo oběma faktory najednou. Obecně platí závislost, čím vyšší působí tlak, tím méně je potřeba vnést teplo a obráceně. Tlakové svařování je označení svařování za působení převážně tlaku a tavné při působení tepla. Svařovat lze kovové i nekovové materiály a materiály podobných i různých vlastností. Pro různé typy spojů a materiálů jsou vhodné různé metody svařování. Při svařování dojde vždy ke změně fyzikálních nebo mechanických vlastností základního spojovaného materiálu v okolí spoje.
Do obchodu s svářecí technikou
Historie svařování
Historicky prvním způsobem svařování bylo svařování kovářské, které se rozvíjelo spolu se zpracováním kovů. Teprve až s rozvojem průmyslu a zvláště s objevem elektrického proudu, vyvstaly požadavky na další způsoby spojování kovů. Velkým impulsem pro rozvoj nových metod svařování – zejména elektrickým obloukem – byly obě světové války ve 20. století. V 60. letech byl využit pro svařování laser a v 70. letech elektronový paprsek pro materiály a konstrukce leteckého a vojenského průmyslu. Poslední vyvinutou metodou – z 90. let minulého století – je třecí svařování promíšením.
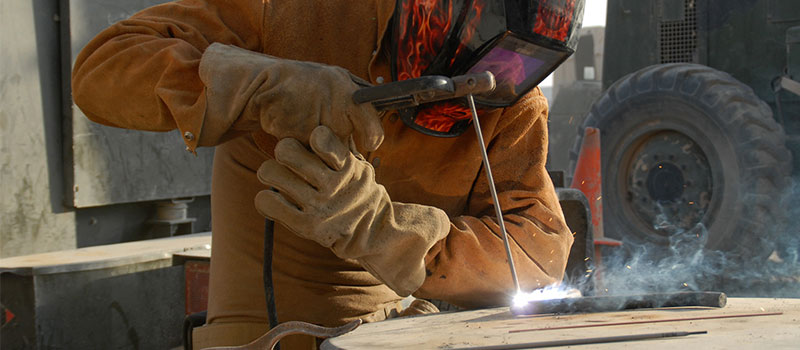
Svářecí metody
U všech svařovacích procesů je účelem spojit zpravidla dva až tři materiály kompaktním spojem – svarem – při působení z vnějšku dodávané energie, která překoná daný termodynamický stav látky. Dodávanou energií může být teplo ( elektrický oblouk, plamen, plasma ), plastická deformace ( tření, výbuch, kovářská činnost ) nebo radiace ( elektronové nebo iontové záření ). Při samotném svařování dochází k interakci mnoha vlivů, například difúze, deformace, rekrystalizace, precipitace, rozpouštění a vznik nových fází, jejichž existence a vývoj závisí na dané použité metodě. Po ukončení procesu svařování vzniká takový spoj, který nelze nedestruktivně rozebrat. To vše za předpokladu kvalitně provedeného svaru. Svařovací metody jsou označování podle ČSN EN 287-1 referenčními čísly ( 111, 135 a mnoho dalších )
Plamenové svařování - autogen, tedy hořící a hoření podporující plyn
Svařování plamenem, zastarale autogenní svařování, je historicky starší metodou než obloukové svařování. Zdrojem tepla plamenového svařování je spalování hořlavého plynu ve směsi s kyslíkem, případně vzduchem. Používají se různé hořlavé plyny pro svařování různých kovů, například:
- kyslík - acetylénové svařování ( metoda 311 podle ISO 4063 )
- kyslík - propanové svařování ( metoda 312 podle ISO 4063 )
- kyslík - vodíkové svařování ( metoda 313 podle ISO 4063 )
Přestože se jedná o jednu z nejstarších metod svařování, její význam ustupuje a v současné době se používá zejména v opravárenství, při renovacích, při klempířských či instalatérských pracích.
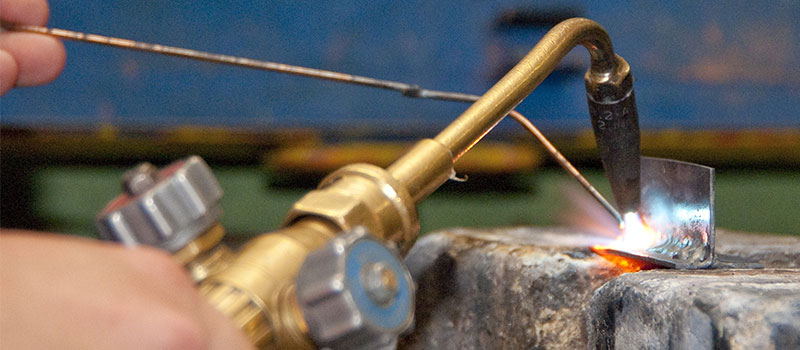
Obloukové sváření obalenou elektrodu MMA - elektrika
Ačkoliv je ruční obloukové svařování obalenou elektrodou ( používaná česká zkratka ROS nebo SOE ; metoda 111 podle ISO 4063 ) nejstarší metodou obloukového svařování, stále si drží nezanedbatelnou pozici v oblasti svařování zejména z důvodu své flexibility, možnosti svařování ve všech polohách, relativně snadné dostupnosti svařovacích zdrojů i přídavného materiálu.
V současné době je její nasazení omezováno z důvodu nízké výkonnosti a nutnosti velmi dobré manuální zručnosti svářeče. Za předpokladu zručného svářeče ale poskytuje metoda vynikající výsledky s ohledem na kvalitu svaru, zvláště v kontextu mechanických vlastností. Srovnatelným svarům se kvalitativně přibližuje snad jen metoda obloukové svařování netavící se elektrodou v ochranné atmosféře inertního plynu.
Výraznou inovací principu této metody je obloukové svařování plněnou elektrodou bez ochranného plynu ( metoda 114 podle ISO 4063 ). Místo elektrody obalenou tavidlem se používá trubičkový drát naplněný tavidlem navinutý na cívce. Tavidlo i v tomto případě zajišťuje vznik ochranné atmosféry. Užití metody 114 není tak časté a používá se spíše pro svařování v polohách jako náhrada za svařování ROS, včetně svařování betonářské výztuže na stavbě.
Obloukové svařování tavícím se materiálem MIG / MAG - v ochranném inertním plynu ( MIG ) nebo aktivním plynu ( MAG )
Pod názvem obloukové svařování tavícím se materiálem v ochranné atmosféře plynu ( MIG/MAG ) se skrývá několik metod založených na stejném principu při použití různých typů svařovacích drátů a ochranných plynů:
- plným drátem v inertním plynu ( v Česku užívaná zkratka MIG; metoda 131 podle ISO 4063),
- plným drátem v aktivním plynu ( v Česku užívaná zkratka MAG; metoda 135 podle ISO 4063),
- plněným drátem v aktivním plynu (metoda 132 podle ISO 4063),
- plněným drátem v inertním plynu (metoda 136 podle ISO 4063).
Tato metoda neklade vysoké nároky na zručnost svářeče díky automatickému podávání svařovacího drátu. Disponuje relativně značným výkonem odtavování ( svařování ) a je s nimi možné svařování ve všech polohách. Lze je použít jak v dílně, tak i na montáži při dosažení slušných podmínek pro svařování s zhruba srovnatelnou kvalitou svaru. Je dostupná široká paleta ochranných plynů i přídavných materiálů. Metody lze snadno mechanizovat a robotizovat. Všechny tyto vlastnosti vynášejí tyto metody na pomyslnou špičku používání v celosvětovém měřítku.
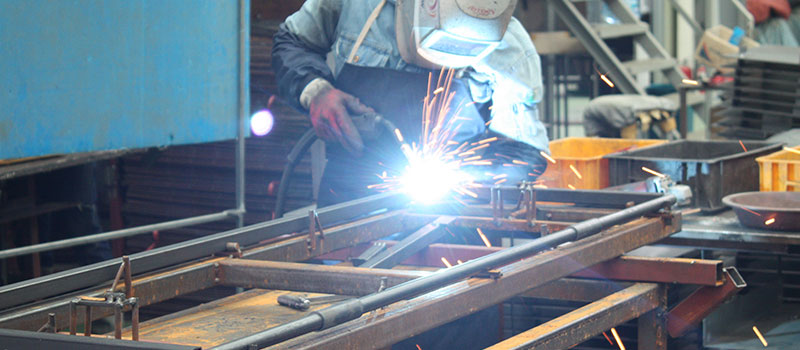
TIG / WIG - netavící se wolframovou elektrodou v ochranné atmosféře inertního plynu a přídavným svařovacím materiálem
Při svařování netavící se elektrodou v ochranné atmosféře inertního plynu ( v Česku používaná zkratka TIG; metody skupiny 141 podle ISO 4063 ) hoří elektrický oblouk mezi netavící se wolframovou elektrodou a základním materiálem nebo svarovou lázní. Jako ochranné plyny se většinou používají argon nebo hélium či jejich směsi. Netavící se elektroda se vyrábí buď z čistého wolframu nebo je legována oxidy dalších kovů.
Dominantním použitím této metody svařování je svařování hliníku, hořčíku a jejich slitin a korozivzdorných ocelí - nerezu, mědi, bronzů, mosazi, titanu, zirkonu, molybdenu a dalších kovů s vysokou afinitou ke kyslíku. Přídavný materiál se přidává ručně, podobně jako u svařování plamenem. Metodou lze provádět velmi kvalitní svary, ale klade vysoké nároky na zručnost svářeče. Výkon odtavení je velmi nízký a nemůže soupeřit s metodami svařování tavícími se elektrodami v ochranných atmosférách.

Svařování pod tavidlem
Metoda automatického svařování pod tavidlem ( používaná česká zkratka APT; metody skupiny 12 podle ISO 4063 ) byla vyvinuta za účelem dosažení vysokého výkonu odtavení při svařování velmi dlouhých svarů při stavbě lodí, mostů, trubek a tlakových nádob z plechů větších tlouštěk. Je to plně automatizovaná metoda obloukového svařování, kdy je svarová lázeň chráněna plyny vzniklými při hoření a tavením tavidla ve svarové lázni. Přídavným materiálem můžou být jak plné dráty ( svařování pod tavidlem drátem; metoda 121 podle ISO 4063 ) tak i svařovací pásky ( svařování pod tavidlem páskovou elektrodou; metoda 122 podle ISO 4063 ), které se ale většinou používají pro navařování.
Svařování atomárním vodíkem
Svařování atomárním vodíkem je jedna z nejstarších metod svařování elektrickým obloukem. Irving Langmuir ji vynalezl během studia chování ionizovaného plynu již v roce 1924. Průchodem proudu vodíku elektrickým obloukem mezi dvěma wolframovými elektrodami dojde k disociaci molekul vodíku. Následná rekombinace atomárního vodíku při dopadu do svarové lázně vede k uvolnění velkého množství tepla. Proud atomárního vodíku – plamen – dosahuje vysokých teplot až 4000 °C. V současnosti se používá jen velmi zřídka – spíše pro speciální aplikace.
Elektronové svařování
Elektronové svařování ( svařování svazkem elektronů nebo svařování elektronovým paprskem ) je metoda používaná pro svařování materiálů vysoce chemicky aktivních ( titan, zirkon, molybden, niob, hafnium, wolfram a podobných materiálů ) nebo vysokotavitelné a žárupevné slitiny jako jsou Inconel či Nimonic.
Jako ostatní tavné metody svařování využívá teplo pro roztavení svarových ploch. Teplo je dodáváno kinetickou energií emitovaných elektronů urychlených vysokým napětím ( 30 až 200 kV ). Průchod elektronů svařovaným materiálem rozvibruje atomovou mřížku, tím dojde k přenosu kinetické energie na tepelnou. Zaostřením svazku lze dosáhnout vysokých hodnot plošné hustoty výkonu v místě působení svazku ( až 5×108 W/mm2 ).
Zásluhou mimořádně vysoké koncentrace výkonu se svazek "protavuje" do hloubky až 400 mm takže umožňuje hluboké a přitom úzké svary v poměru až 50:1. Někdy se pro to používá výraz "klíčová díra" pro charakteristický tvar svaru. Lze svařovat ve vakuu ( metoda svařování 511 podle ISO 4063 ), v okolní atmosféře ( metoda svařování 512 podle ISO 4063 ), případně v atmosféře ochranných plynů ( metoda svařování 513 podle ISO 4063). Vakuum, ve kterém se svařování uskutečňuje, má jednak příznivé rafinační účinky na vlastnosti svaru a jednak dokonale chrání svarovou lázeň před účinky okolní atmosféry. Přídavný materiál se zde používá jen velmi zřídka.
Aluminotermické svařování
Aluminotermické svařování, jinak též svařování termitem, se používá především ke svařování kolejnic. V tyglíku s otvorem ve spodní části, umístěném nad svařovaným místem, se pomocí magnéziové roznětky zapálí směs oxidu železitého a hliníkového prášku. Při chemické reakci se dosáhne teplota cca 2450 °C – vzniká tekuté železo a na něm struska oxidu hlinitého.
Tlakové svařování
Tlakové svařování je charakterizováno působení jak tlaku tak tepla a to za vzniku plastických deformací a ke spojení dochází i při částečně natavených materiálech.
Odporové svařování
Odporové svařování ( metody skupiny 2 podle ISO 4063 ) se používá pro spojení dvou materiálů položených na sobě. Tato metoda se nejčastěji používá k bodování ocelových plechů nebo spojení drátů do mříží, tedy sítí. Spojované materiály jsou k sobě přimáčknuty dvěma elektrodami jimiž zároveň prochází elektrický proud. Ocel je oproti měděným elektrodám špatný vodič, proto v ní při procházení proudu vzniká velký odpor a dojde k lokálnímu ohřátí styčných ploch svařovaných plechů.
Při současném působení tlaku tak dojde k lokálnímu svaření. Vzniklé svary mají velkou pevnost proti usmýknutí ve směru ploch plechů ve srovnání s namáháním kolmo k povrchu plechů. Přítlačná síla se pohybuje v hodnotách 500 až 10 000 N, svařovací proud 1 až 100 kA při délce působení 0,04 až 2 s.
Nejčastěji se užívá bodového odporového svařování ( metoda 21 podle ISO 4063 ), při kterém vznikne svar přibližně o velikosti elektrod. Při švovém odporovém svařování ( metoda 22 podle ISO 4063 ) se spojují plechy dlouhým svarem za pohybu kotoučových elektrod.
Elektrody se vyrábějí z takových materiálů, které lze nekonfliktně použít pro svařování daných základních materiálů. Pro ocelové plechy a dráty se nejčastěji používají měděné, které při vývinu tepla neuvolňují do okolního prostředí žádné škodlivé plyny. Jinými materiály elektrod mohou být například slitiny kobaltu a kadmia, mědi a stříbra a kadmia, mědi a niklu či křemíku
Odporové svařování nachází uplatnění jak v mechanizovaných a robotizovaných pracovištích při sériové výrobě - ve výrobnách karosérií, tak i v malosériových provozech.
Svařování třením
Třecí svařování ( metoda 42 podle ISO 4063 ) využívá tepelné energie vzniklé při tření dvou ploch. Po přípravě svarových ploch - srovnání a očištění je jedno těleso upevněno k stacionární části a druhé těleso je připevněno k rotační části. Druhé těleso se roztočí a působícím tlakem v ose rotace se přitlačí ke stojícímu tělesu. Na kontaktní ploše mezi oběma tělesy vzniká za působení tření vysoká teplota, zhruba na úrovni 80 až 85 % teploty tavení a oba materiály na kontaktu zplastizují při současném působení tlaku. Během svařování dojde ke vzniku takzvaného výronu, který se většinou odstraňuje.
Kovářské svařování
Velmi dlouhá historie kovářského svařování jej učinila všestrannou metodou pro spojování stejných i různých kovů. Ke spojení dochází při zahřátí kovů na teplotu zhruba 50 % až 90 % teploty jejich tání a působením vnějšího tlaku - údery kladiva nebo lisu na materiál. Difúzní procesy jsou díky zvýšené teplotě urychleny a dochází tak ke snadnějšímu vytvoření pevného spoje.
Techniky kovářského svařování bylo využíváno pro výrobu takzvané damascenské oceli při níž je plát oceli opakovaně nahřát, přehnut na sebe a kladivem nebo lisem rychle svařen. Tento postup vede k výrobě velmi pevné ale zároveň houževnaté oceli.
Difuzní svařování
Difúzní svařování ( metoda 44 podle ISO 4063 ) je založeno na teorii Fickových zákonů, které popisují difúzní tok atomů, jejich koncentraci a rychlost změny koncentrace v závislosti na vzdálenosti atomů. Svařovací proces probíhá kontaktem dvou hladkých ploch, které jsou ohřáté na 50 až 90 % teploty tání a působením tlakové síly.
Po kontaktu dvou ploch nastává plastická deformace při přemisťování vakancí a dislokací a poté difúznímu procesu, který vede na vyrovnání energetické bilance a tak vymizení původního rozhraní ploch. Difúzní svařování dává vysoce kvalitní spoje bez negativních vlivů tavného svařování, jako jsou vnitřní pnutí a deformace nebo tepelně ovlivněné oblasti. Velmi často se difúzní svařování provádí ve vakuu při svařování materiálu s vysokou afinitou ke kyslíku, například titanu a jeho slitin.
Svařování výbuchem
Výbuchové svařování ( metoda 441 podle ISO 4063 ) se používá zejména pro navařování - plátování. Dvě desky se na sebe položí, na horní povrch horní desky se rozprostře výbušnina, která se přivede k explozi. Rázová vlna, která kovem prostupuje způsobí tlak 10 až 100 GPa, který je mnohonásobně větší než mez kluzu spojovaných materiálů ( nízkolegovaná ocel dosahuje meze kluzu řádově 102 MPa ). Tlaková energie se tak přemění na deformační, oba materiály na kontaktní ploše zplastizují. Dochází tak k chování, které se popisuje hydrodynamickou teorií ideální kapaliny.
Pro vytvoření dobrého spoje je nutná rychlost exploze nižší než rychlost šíření zvuku spojovaných materiálů.
S výhodou se výbuchové svařování používá pro svařování různých materiálů, které metodami tavného svařování nelze spojovat, třeba ocel a titan.
Svařování ultrazvukem
Ultrazvukové svařování ( metoda 41 podle ISO 4063 ) využívá mechanického rozkmitání o vysoké frekvenci při současném působení tlakové síly, která zaručuje přenos kmitů z sonotrod do spojovaných materiálů. Rozkmitáním dochází i k relativně malému ohřevu v dané oblasti a vzniku plastických deformací. Ultrazvukové svařování našlo své uplatnění zejména při svařování plastů, ale také při svařování vodičů, například u vícežilových kabelových svazků.
Svářeč nebo svářečka
Osoba, která se profesně zabývá svařováním kovů, se označuje jako svářeč. Takový svářeč potřebuje mnoho nástrojů, pomůcek a vybavení jednotně nazývanou jako svářecí technika. Jedná se o přídavné svařovací materiály jako dráty navinuté na cívce nebo volně v tyčích - plné či trubičkové a elektrody obalené, neobalené či wolframové elektrody. Přídavné svářecí materiály mohou být ocelové, litinové, nerezové, hliníkové, pozinkované, poměděné a jiné. Na tavné sváření přídavných materiálů se použije vhodná svářecí metoda a k tomu svářecí technika. Nejlépe svářečka, neboli svářecí zdroj s vhodnou svařovací metodou.
Svářecí a svařovací technika
K svářečce však potřebuje svářeč i další vybavení, jako svářecí hořák, svařovací kabely, držák elektrod, zemnící svěrku, redukční ventil, hadice, rukojeti, spojky a mnoho dalšího vybavení, náhradních a spotřebních svářecích materiálů, pomůcek a chemie. Vhodná chemie pro svaření pomáhá i chrání - separační spreje, kapaliny, pasty, gely. V poslední fázi je nutné a velmi důležité kvalitně chránit samotného svářeče. K tomu slouží svářečské oblečení - boty, kalhoty, kabáty, rukavice a ochrana hlavy a obličeje. Zejména k ochraně očí a dýchacích cest se používají svářecí kukly a to samostmívací svářecí kukly - samozatmívací svářecí kukly pro všechny metody sváření a jako ochrana očí obličeje při svařování nebo broušení.
Používá se mnoho výrazů jako stmívací svářecí kukla, samozatmívací kukla, stmívací svařovací kukla, samozatmívací svářečská kukla, automatická kukla pro sváření, kukla svářečská, svařovací samostmívací kukla, zatmívací svářecí kukla, svářecí helma, kukla pro TIG a mnoho a mnoho dalších výrazů. Stejně tak ostatní svářecí technika a pomůcky se mnohdy označuje slangovými výrazy. Slovník svářeče a svářečky, ale všechny slangové výrazy rychle a jednoduše vysvětlí.
Kvalita svařování
Během svařování se vytváří takové termodynamické podmínky, při kterých snadno zanikají staré a vznikají nové strukturní vazby. Obecně lze svařování popsat jako proces změny vnitřní struktury jak základního tak přídavného materiálu za účelem získání trvalého a nerozebíratelného spoje.
Ačkoli se mnoho materiálů vhodných pro svařování jeví z makroskopického hlediska jako homogenní, jsou z hlediska strukturního na mikroskopické úrovni ( na úrovni krystalové mřížky ) heterogenní. Obzvláště patrné je to u ocelí, nebo slitin s omezenou rozpustností složek v tuhém roztoku ( například binární diagram železo - uhlík ). Přirozeně proto lze očekávat, že u takových materiálů bude i struktura svarového kovu heterogenní.
Z důvodů popsaných dále, lze za kvalitní svar považovat takový svar, který beze zbytku splní požadavky na něj kladené.
Vady ve svarech
Během svařování se mohou vyskytnout okolnosti, které vedou k vzniku nedokonalostí a vad svaru. Druhy vad jsou většinou typické jak daným svařovaným materiálům tak metodám svařování. Vady jsou normativně hodnoceny, tedy kvantifikovány a kvalifikovány na základě daných kritérií pro daný typ výrobku.
ČSN EN ISO 5817 pro oceli, nikl, titan a jeho slitiny
ČSN EN ISO 10042 pro hliník
Jiná kritéria jsou nastavena pro výrobky a konstrukce, jejichž případný kolaps má minimální dopad na majetek, zdraví či životy osob, třeba zábradlí a jiná platí pro oblast, ve které může relativně drobná chyba způsobit katastrofální následky, například jaderná elektrárna.
Vodíkem indukované trhliny za studena vznikají především u feritických a martenzitických ocelí za přítomnosti difúzního vodíku ve svaru, který se dostal do svarové lázně buď z okolní atmosféry při nedokonalé plynové ochraně nebo ze znečištěných svarových ploch nebo z vlhkých obalů elektrod či kombinací těchto vlivů. Impulsem často bývá i vysoká hladina reziduálních pnutí. Tyto trhliny se zjišťují po vychladnutí svaru nebo delším časovém období - třeba po jednom dni.
Trhliny za horka vznikají především v austenitických typech ocelí ( korozivzdorné chrom niklové oceli ). Za jejich vznikem je přítomnost nečistot síry a fosforu, které tvoří sloučeniny s železem. Ty mají nižší bod tavení a působí při chladnutí kovu vznik reziduálních napětí a tím porušení krystalové mřížky.
Zápaly, studené spoje a koncové krátery jsou typické vady způsobené svářečem.
Póry a bubliny nebývají časté u svarů ocelí, kdy jsou způsobeny spíše špatným technologickým postupem, přirozeně se vyskytují pouze při svařování oceli s povlakem zinku. Typické jsou pro materiály s vysokou afinitou ke kyslíku, tedy hliník a jeho slitiny, měď, ale i titan a jeho slitiny.
Trhliny, zápaly, studené spoje a koncové krátery se v dynamicky namáhaných konstrukcích jako jsou dopravní prostředky, některá strojní zařízení, mosty a další konstrukce se nesmí vyskytovat, neboť mohou vést k iniciaci a šíření únavové trhliny, která může způsobit náhlý kolaps.
Legislativa a požadavky na svar
Výrobkem je jakákoliv věc, která byla vyrobena, vytěžena nebo jinak získána bez ohledu na stupeň jejího zpracování a je určena k uvedení na trh jako nová nebo použitá.
Z hlediska naplnění kvality je svařování činnost, která se podílí na vzniku výrobku. V souladu se zákonem číslo 22/1997 Sb. je nutné mít pro výrobu zavedený systém zabezpečení a řízení jakosti, který je definovaný v normách ISO 9001. Podle ČSN EN ISO 9001 je svařování takzvaný validovaný proces, u kterého nelze jakost zajistit pouze na základě kontroly a zkoušek. Jakost tohoto procesu musí být plánovitě zajišťována od počátku výroby až po předání výrobu odběrateli či spotřebiteli.
Pro svařování byla zavedena jako dodatečný nástroj k procesům výroby ISO 9001 ještě norma ČSN EN ISO 3834, která upravuje požadavky a postupy při svařování na základě písemných instrukcí, tedy specifikací postupů svařování ( WPS ).
Specifikace postupu svařování je dokument, který definuje jednotlivé proměnné jako jsou svařovací proud a napětí, rychlost podávání drátu, průtok ochranného plynu a mnoho dalších specifik pro danou svařovací metodu, materiál, typ svaru a další a to tak, aby byla zajištěna opakovatelnost. WPS použité při výrobě by měly být podloženy dokumentem kvalifikace postupu svařování ( WPQR ), který vydává certifikovaný orgán na základě pWPS ( to je předběžná WPS ) a na základě výsledků destruktivních zkoušek svarového spoje.
Dalším požadavkem na zajištění jakosti procesu je i zabezpečení výroby kvalifikovanými pracovníky, a to jak svářeči tak odpovědným svářečským dozorem.